こんにちは。技術チームの高崎です。
今月も技術チーム内で技術勉強会を開催したので、その内容をお伝えしたいと思います!
今回は技術チームマネージャーの赵 玉圭さんによる、GAS(Gate Assort System: ゲートアソートシステム)の勉強会でした。
■GASとは?
GASとは主に物流の現場で利用される、「仕分け」業務の自動化・効率化を実現するためのシス
テムです。
実際のものはこんな感じのデザインをしています。結構大きいですね。
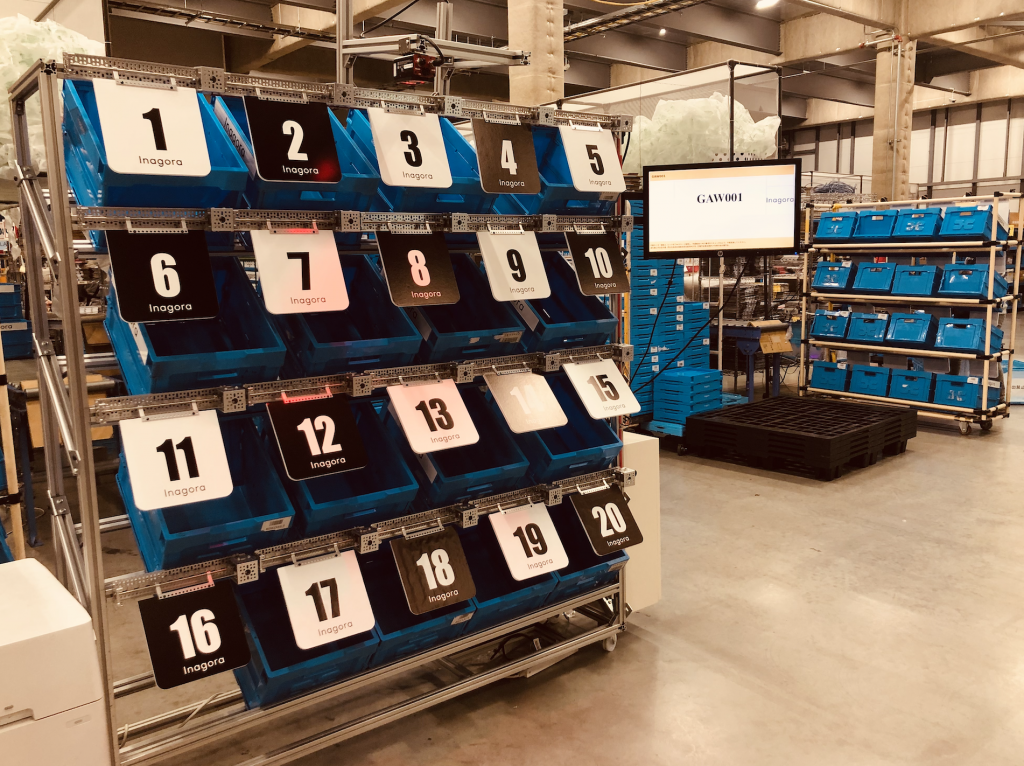
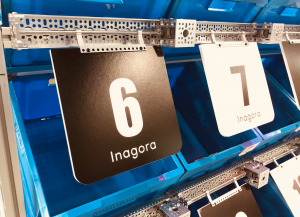
計20個のゲートと商品を仕分けるためのオリコン、それを固定するメインフレームから構成されています。
昨年弊社技術・物流チームはこの設備の設計~開発を行いましたが、その導入に至った背景に関して、まず説明します。
■導入背景
弊社は海外向けECサービスを運営していますが、ユーザへの最適な配送のためには、適切な在庫管理、発注や商品配送業務の最適化は欠かせません。そのため弊社では、業務に関わるほぼ全てのシステムを全て内製化し、要件定義からリリース運用まですべて社内で一気通貫で行っています。
倉庫管理システムを作ったり、商品のピッキング作業を行うためのAndroidアプリ開発を行っていましたが、初期のリリースから4年ほど経ち、問題も発生していました。
例年ダブルイレブンキャンペーン(毎年11月11日に開催される中国大手ECのセールキャンペー ン。昨年の流通総額は4,982億元(約7兆7,200億円)を記録しました。https:// www.alibaba.co.jp/news/2020/11/gmv7ecgmv.html)の際には、一時的に需要が急増しますが、その際に倉庫対応の人員を急増させたとしても、業務の習熟度の差から、生産効率が思いの外上がらなかったり、現場社員の負担が大きくなるなど、対応が急務となっていました。
この問題への対策として、GASシステムの導入&開発が検討されました。
元々のピッキング(商品を倉庫から探す)&リビング(探した商品を発注単位で仕分ける)業務は以下の様なフローになっていました。
1. 発注情報をSCM(サプライチェーン・マネジメント・システムの略。在庫数・各商品のロケーションを管理する)より取得。作業者のPDA(作業情報端末)へ保存。
2. 発注情報からピッキング対象商品が決定。ロケーションが指示される
3. ピッキング対象商品をスキャニング&リビング対象ケース指定
4. 商品をリビング。仕事が終わると1へ戻る。
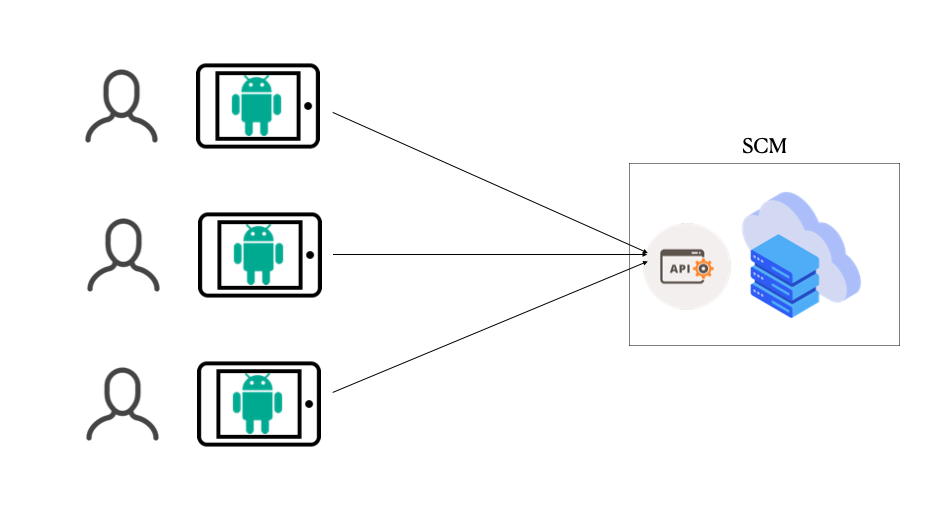
既存のシステムの場合、
・API通信の回数が多く、スキャニングから、情報の取得までレイテンシーが発生してしまうこと。(特に倉庫の作業が集中する期間が顕著)
・倉庫内の場所によっては、電波が不安定な箇所があり、都度APIを呼び出しすることが業務に影響する可能性があること。
・PDAの操作性の問題からある程度の習熟コストが発生すること。
など、複数の問題が存在していました。上記の問題を業務フローレベルから改善するために、弊社の業務に合わせたGASをハードウェアから設計&開発するプロジェクトが立ち上がりました🔥
■GAS導入後の新ワークフロー
GASを導入することで大きく変わる点は、これまで作業者が一連の中で行っていたピッキングとリビング業務を分離出来ることです。倉庫内の作業は単純化すれば必要な商品を探して発注毎に仕分け、梱包し発送する業務ですが、倉庫内の敷地は広く、また商品点数も多いため商品を探すだけでもコストが発生します。
そこで最も時間のかかっていたピッキング業務とリビング業務を分離し、リビング業務をGAS側で担当し自動化することで生産コストの削減を図りました。
■GASの構成要素
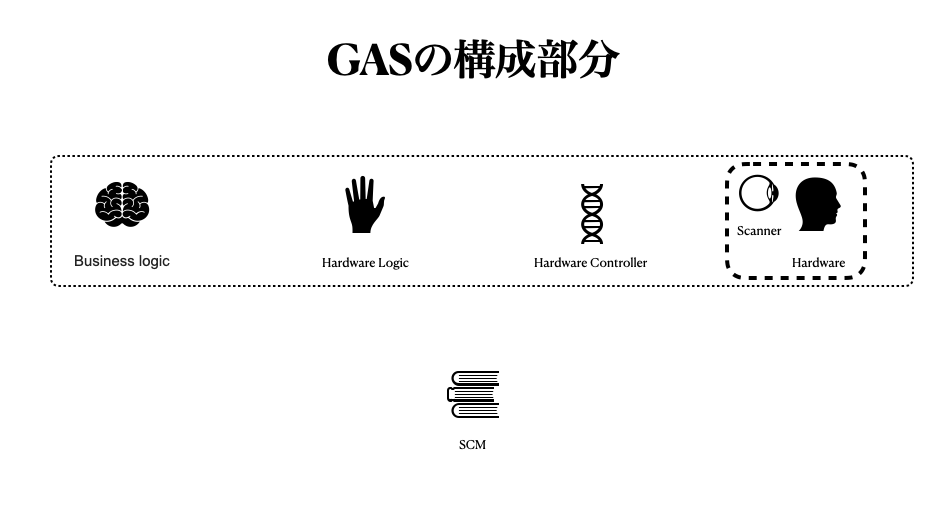
GASは主に、4つの構成要素から成ります。
Business Logic: ゲートの開閉ロジックなど。ハードウェアを実行するコマンドをHardware ControllerにUSB経由で送信
Hardware Logic(Arduino)+ Hardware Controller: コマンドを実行&Hardwareを操作Scanner + Hardware: 商品JANCODEの読み込み、ゲートを開閉するモーターなど
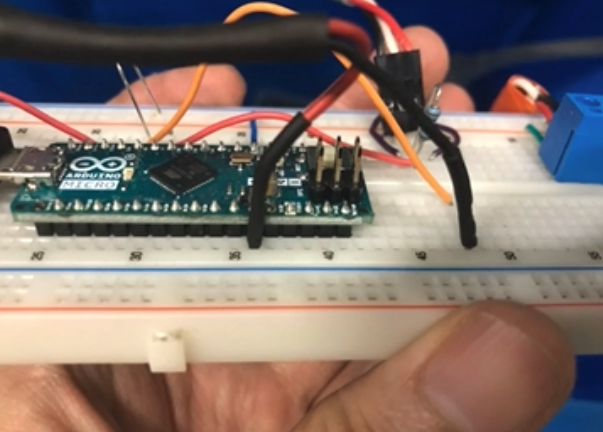
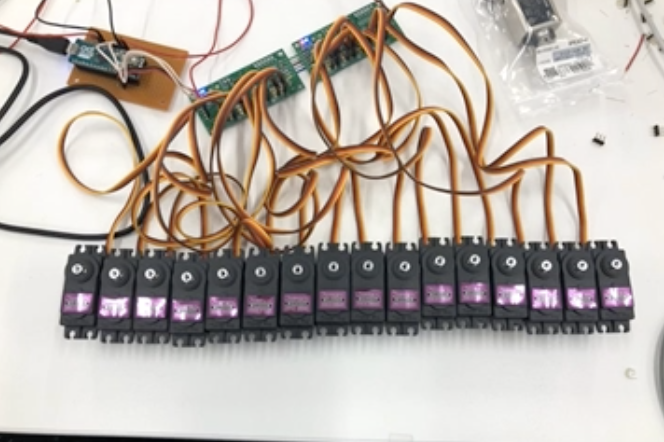
■GASのワークフロー
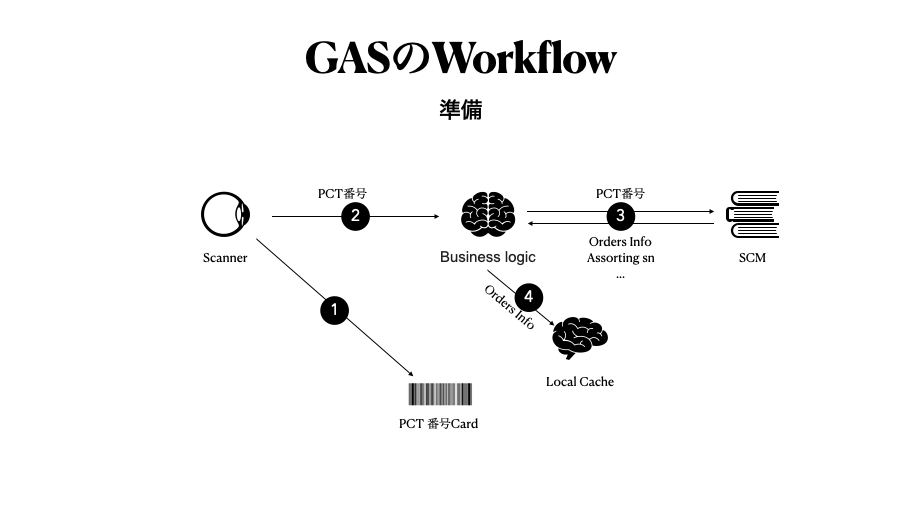
ワークフローは以下の通りです。
1. PCT番号(ピッキングした台車)をGAS付属のスキャナでスキャニング。
2. 3. スキャニングした情報を元にSCMAPIを呼び出す。発注情報などを取得。
4. 取得した発注情報とをGASローカルにキャッシュ(この際に、1でスキャンしたオリコンと発注情報からどの発注を、どのオリコンに入れるかマッピングを行います。)
これでこれまでは都度APIを呼び出して取得していた情報を全て取得し、ローカルにキャッシュ出来ました。これでリビング作業の準備段階が完了です。
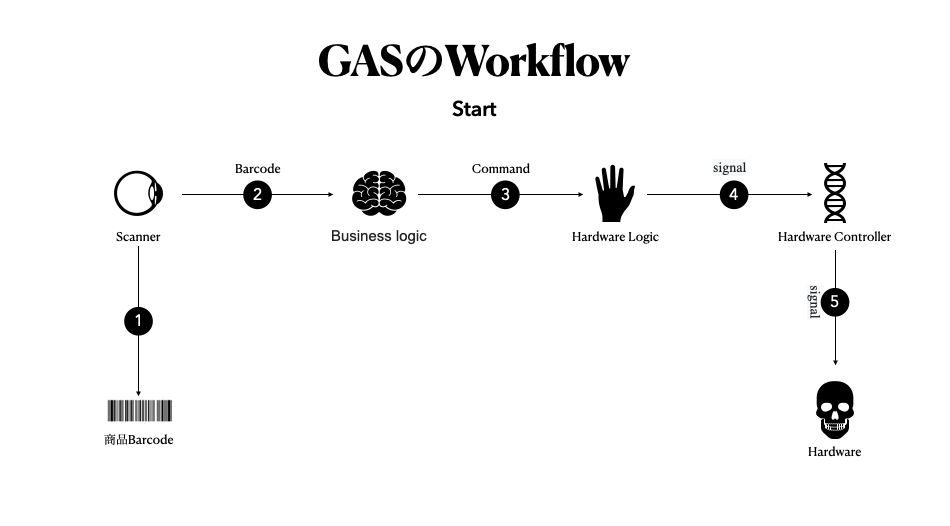
次に実際にリビングを行います。
1. ピッキングされてきた商品バーコードをスキャニング。
2. バーコードをGAS側で受信。準備段階でキャッシュした発注情報と照合。
3. 4. 5. 照合結果から、該当のオリコンを特定。ハードウェアを制御して、対象のオリコンの
ゲートをオープン🚪 オープンしたゲートに商品を入れる。
上記の様にGASの操作者は、商品をスキャンするだけで、何も考えずリビング作業を出来る様になりました。これならすぐに慣れない作業者でも現場で活躍できそうです🔥
このGASシステムは昨年の弊社のダブルイレブンキャンペーンでも使用され、生産効率の上昇に大きく寄与しました🎉
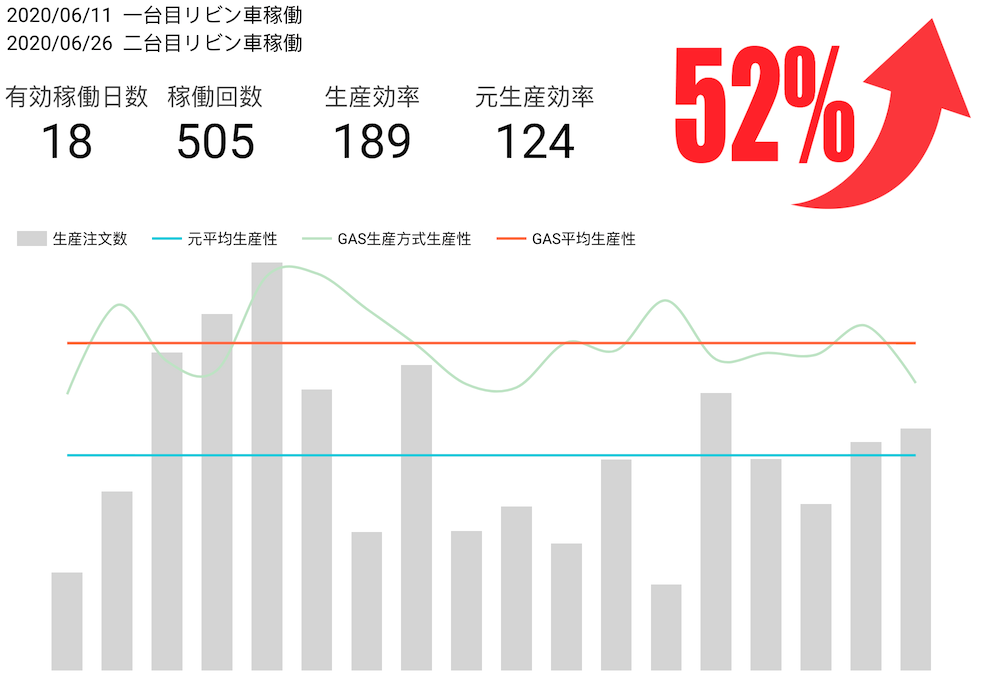
ただ現状ハードウェア特有の問題も残されています。例えば、ゲート部分のネジが一定稼働後にはやや緩んでしまう問題があり、そうなるとゲートを開く速度に影響がでてしまいます。なので、現状は定期的に現場で目視によるメンテナンスを行い、対応しています。。
GASは東京技術チームにとって初めてのハードウェアプロジェクトでしたが、部門を超えた協力を経て、無事にリリース&成果を出すことが出来ました。今後もどんどん新しい領域に挑戦して新しい技術を現場に活かしていきたいです。
最後にInagora技術チームでは、ソフトウェアだけでなくハードウェアのエンジニアリングをしてみたいエンジニアも募集中です。よろしくお願いします。
サーバーエンジニア (PHP)
https://www.inagora.com/recruit/carrier/server-engineer-php/